Making Best Use Of Performance and Quality With Cutting-Edge Steel Stamping Techniques
In the realm of metal stamping, the search of operational excellence through the combination of cutting-edge strategies is vital. The junction of innovative metal stamping approaches, automated systems, strict high quality controls, and lean production principles offers a tantalizing look right into the future of manufacturing.
Advanced Metal Stamping Technologies
In the world of steel marking, the assimilation of advanced innovations has actually reinvented the market, enhancing precision and efficiency in manufacturing procedures - Metal Stamping. Advanced steel marking innovations have played an essential role in raising the abilities of producers, enabling even more elaborate layouts and greater manufacturing rates
One of the most considerable improvements in metal stamping technology is the application of computer numerical control (CNC) systems. CNC systems make it possible for specific control over the stamping process, causing accurate and regular manufacturing of complicated parts. In addition, making use of servo presses has actually caused improvements in energy efficiency and lowered cycle times, additionally enhancing the manufacturing procedure.
In addition, the integration of automation and robotics has structured steel marking operations by increasing performance and reducing the danger of errors. Automated systems can execute tasks with rate and accuracy, leading to improved overall efficiency in the production line.
Automated Procedures for Efficiency
Use of automated processes in steel stamping operations has considerably boosted efficiency and performance in producing centers (Metal Stamping). Automated systems have transformed the steel stamping market by streamlining processes, decreasing hand-operated intervention, and decreasing the margin of error. These automated options include a range of modern technologies, including robot arms, CNC machines, and computerized control systems, that work cohesively to implement elaborate marking jobs with precision and rate
One primary advantage of automated procedures in metal marking is the regular quality they provide. By getting rid of human mistake and variations in production, automated systems make certain that each stamped part meets precise requirements with marginal problems. Automation allows constant procedure, dramatically lowering downtime for tool modifications and upkeep, consequently making best use of overall productivity.
Additionally, automated procedures improve safety and security in steel marking operations by reducing the need for manual handling of sharp devices and hefty products. This not only safeguards workers however likewise adds to an extra structured and effective workflow. To conclude, the integration of automated processes in metal marking procedures is critical for attaining ideal effectiveness, high quality, and safety and security criteria in contemporary manufacturing settings.
Top Quality Control Procedures in Stamping
Given the emphasis on regular high quality and effectiveness achieved via automated procedures in metal stamping procedures, carrying out robust quality control actions ends up being vital to support standards and guarantee precision in stamped components. Quality assurance in metal marking involves a multi-faceted approach to ensure the reliability and precision of the final products. Inspection checkpoints at numerous phases of the stamping process are important to recognize any discrepancies from requirements at an early stage. Making use of sophisticated modern technologies such as computerized vision systems and automated dimension devices can improve the rate and accuracy of quality evaluations. Analytical process control techniques aid in monitoring and managing index the marking procedure to detect any type of variations that can impact top quality. In addition, training programs for staff on quality requirements and procedures are crucial to make sure that every person entailed understands and follows the established quality assurance methods. By integrating these measures into steel stamping operations, makers can continually generate top quality stamped parts that satisfy the rigid requirements of contemporary markets.
Enhancing Accuracy With Technology
To attain unmatched accuracy in metal marking procedures, pioneering developments are continually being created and integrated into the production operations. Advanced innovations such as laser cutting systems and computer system numerical control (CNC) makers have changed the method steel elements are stamped with utmost precision. By making use of laser reducing innovation, suppliers can accomplish complex and detailed styles with micron-level precision, ensuring that each stamped component meets the strictest quality criteria.

Additionally, using simulation software application allows producers to evaluate and enhance stamping processes prior to real manufacturing, determining potential areas for improvement and fine-tuning parameters to attain optimum precision. By embracing these ingenious innovations, makers can improve precision, increase efficiency, and deliver top notch stamped products that meet one look at this website of the most rigid demands of modern markets.
Executing Lean Manufacturing Practices
Integrating lean manufacturing methods right into metal stamping procedures can lead to streamlined manufacturing processes and raised general performance. By focusing on removing waste, optimizing sources, and continuously enhancing procedures, metal marking companies can improve performance and quality while minimizing prices.
Additionally, lean production practices encourage a society of continual enhancement within the organization. By empowering workers to identify and deal with inefficiencies, business can make step-by-step changes that bring about considerable efficiency gains over time. Executing devices such as five, Kanban systems, and value stream mapping can assist streamline operations, lower preparations, and enhance general high quality in steel marking procedures.
Conclusion
In conclusion, the usage of sophisticated metal stamping innovations, automated procedures, quality assurance actions, technology for accuracy improvement, and application of lean manufacturing methods are critical description for optimizing performance and top quality in steel marking procedures. These approaches ensure that products are produced with cost-effectiveness, uniformity, and accuracy. By integrating these advanced techniques, manufacturers can stay affordable in the market and satisfy the demands of customers effectively.
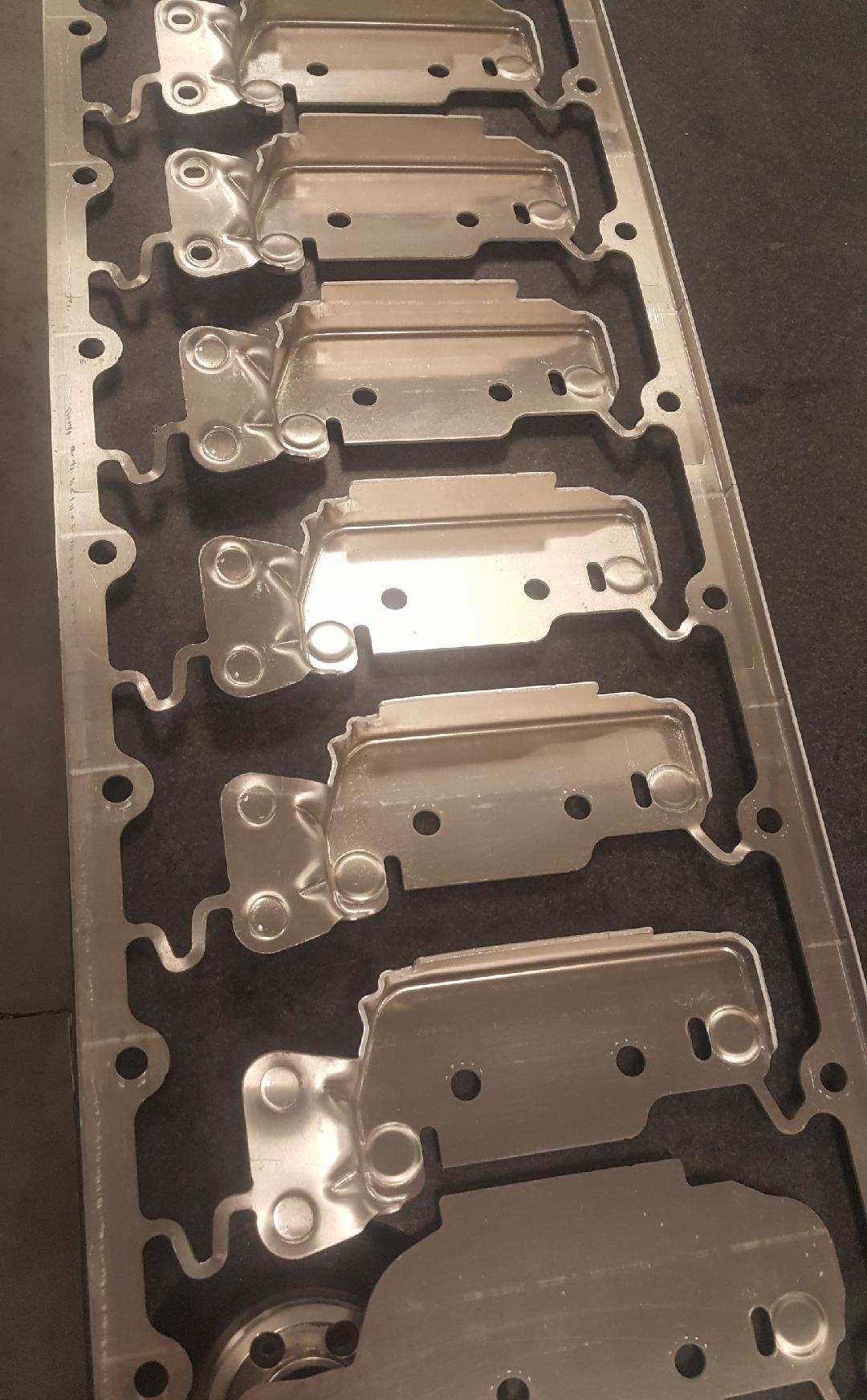
Offered the focus on consistent quality and effectiveness attained via automated processes in steel marking operations, applying durable high quality control actions becomes critical to make certain and promote criteria accuracy in stamped components. Applying devices such as Five, Kanban systems, and worth stream mapping can aid simplify procedures, lower lead times, and boost total top quality in steel stamping processes.
In conclusion, the usage of sophisticated steel stamping innovations, automated processes, high quality control steps, development for precision enhancement, and execution of lean production techniques are crucial for making best use of performance and high quality in metal stamping procedures.